
Product display
-
Position > Home > Product display >
-
Product name: pvc
Product model:
- Product description
- 一、:
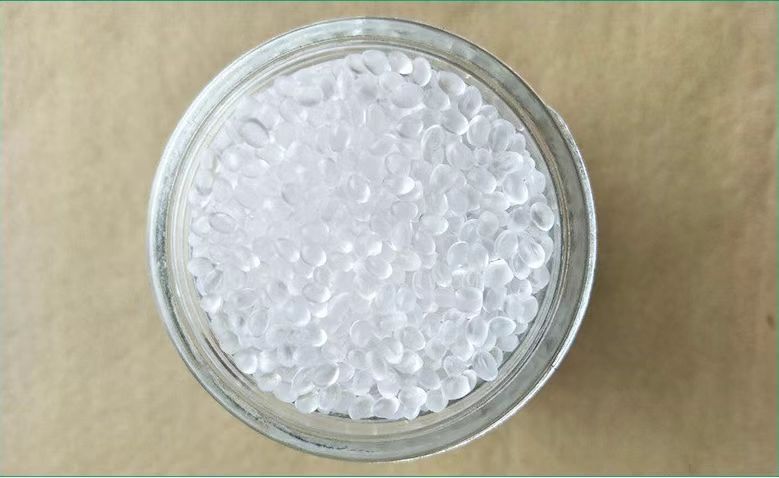
The production of LLDPE begins with transition metal catalysts, especially Ziegler or Phillips types. New processes based on cycloolefin metal derivative catalysts are another option for LLDPE production. The actual polymerization reaction can be carried out in a solution and gas phase reactor.
In general, octene and ethylene are copolymerized in a solution phase reactor, butene. Hexene and ethylene were polymerized in a gas phase reactor. LLDPE resin produced in a gas phase reactor is in granular form and can be sold as powder or further processed into pellets. A new generation of super LLDPE based on hexene and octene has been made from Mobile, combined carbide. Launched by companies such as Novacor and Dow Plastics. These materials have a large toughness limit and have new potential in the application of automatic bag removal. Very low density PE resin (density below 0.910 g/cc) It has also appeared in recent years. VLDPES has a flexibility and softness that LLDPE cannot achieve. The characteristics of the resin are generally reflected in the melting index and density. The melting index can reflect the average molecular weight of the resin and is mainly controlled by reaction temperature. The average molecular weight is independent of molecular weight distribution (MWD). Catalyst selection affects MWD. The density is determined by the concentration of the copolymerized monomer in the polyethylene chain. The monomer concentration of copolymerization controls the number of short branched chains (the length of which depends on the type of monomer used for copolymerization) and thus controls the resin density. The higher the concentration of copolymerization monomer, the lower the density of resin. Structurally, LLDPE differs from LDPE in the number and type of branched chains, with high voltage LDPE having long branched chains, while linear LDPE has only short branched chains.
Structurally, LLDPE differs from HDPE only in the number of short branched chains. HDPE has fewer short branch chains and, therefore, is a higher density material. The physical properties of LLDPE are controlled by its molecular weight, MWD and density. LLDPE is superior to LDPE in the final analysis, depending on its use. In general, LLDPE is used in all applications to produce more rigid products, although both LLDPE and LDPE have densities between 0.91 and 0.925 according to the ATSM standard for low-density materials. LLDPE forms a higher crystalline structure because there are no long branched chains. The larger crystallinity of LLDPE produces a product with higher rigidity. This higher crystallinity also increases the melting point of LLDPE by 10~15℃ compared with LDPE. Higher tensile strength, resistance to penetration, tear resistance and increased elongation are the characteristics of LLDPE, making it particularly suitable for thin films. If hexene or octene is used instead of butene as a copolymer, even the impact resistance and tear resistance can be greatly improved. For a given resin with the same melt index and density, hexene and octene LLDPE resins improve impact and tear performance by up to 300%. The longer side chains of hexene and octene resins act like "knot" molecules between the chains, improving the toughness of the compounds. Resins produced with cycloolefin metal derivative catalysts will have unique properties. The narrower MWD, improved copolymer distribution, and better film transparency, sealing and impact strength are similar to LLDPE produced with Ziegler catalyst. In terms of transparency, LLDPE has similar shortcomings to LDPE. The turbidity and gloss of LLDPE film are not good, mainly because of its higher crystallinity, which causes the surface roughness of the film. The transparency of LLDPE resin can be improved by blending with a small amount of LDPE.